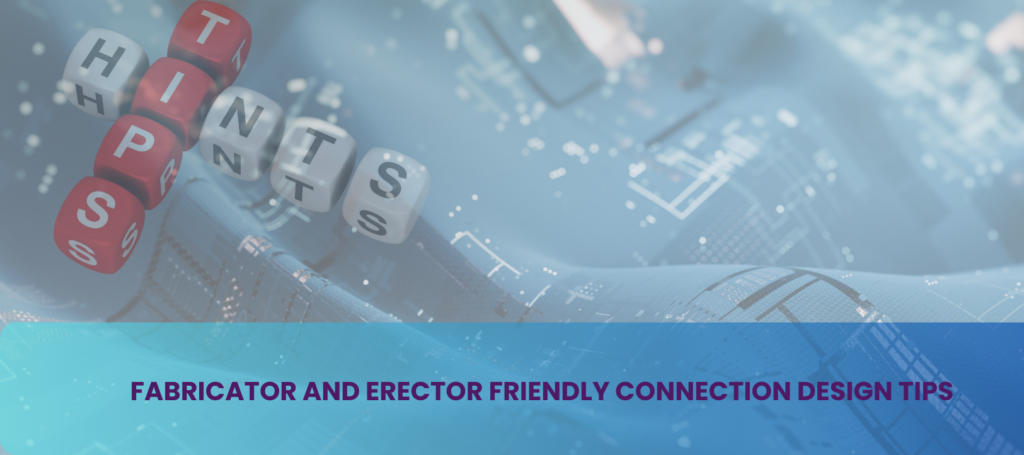
If you’re looking for the best connection design services in India, it’s crucial to understand that each fabricator has a preference for a standard connection based on shop equipment, ease of erection, and specified shear reactions. When designing connections, consider the following connection design tips to ensure your project is completed efficiently and effectively.
Send Us Your Fabricator Preferences
1) Prefer shear plate connections for beam-to-column flange-plated moment connections:
When flange plates need to be welded to a column flange, using a shear plate connection is highly advantageous. This approach simplifies the process, as the column can be easily positioned in the shop for welding the flange plates. Additionally, the shear plate can be readily welded in this setup, ensuring a strong and stable connection.
2) Avoid using slotted holes in plates thicker than the bolt diameter:
Slots in thick plates are costly due to the flame-cutting process. It’s better to prefer standard or oversized holes, which are more efficient and economical.
3) In bolted flange-plated connections, the flange plate should be wider than the beam flange:
For connection design tips, always allow at least a ½” margin on each side of the flange plate in bolted flange-plated connections. This provides a sufficient shelf dimension to accommodate longitudinal fillet welds if bolt holes misalign in the field, compensating for any missing bolts.
4) Avoid overhead welding:
The preferred welding positions are flat and horizontal. Overhead welding is challenging, costly, and often results in lower-quality welds, making it less ideal for the best connection design services in India.
5) Specify slip-critical bolts only when required:
Slip-critical bolts are not always necessary for moment and brace connections; bearing bolts in standard holes may be acceptable. Slip-critical bolts are more expensive due to additional installation, inspection, and faying-surface preparation involved.
6) Provide Bolted HSS Brace connection:
HSS braces are commonly shown slotted and welded to the gusset plate. To eliminate the field-weld, the HSS brace can be bolted to the gusset plate. A slotted HSS/gusset-plate connection could be used for a more efficient design.
7) Use Face-mounted shear plate connections whenever possible with HSS Columns:
Avoid through-plate shear connections, which are costlier than face-mounted single-plate connections. Opting for face-mounted shear plate connections can save time and resources.
8) Avoid Moment connections with HSS Columns:
Moment connections to HSS columns typically cost a lot of money. It’s often more economical to consider alternative connection designs.
9) Provide optimized connections:
The cost of fabrication and erection increases with the number of components in a connection detail. Prefer AISC standard connections whenever possible, as they offer optimized designs that align with the best connection design services in India.
10) Review member sizes to optimize connection costs:
- Ensure perimeter beams have sufficient flange width to support the deck and pour stops and accommodate welding studs.
- Use larger columns to eliminate the need for stiffener plates and web doubler plates at moment connections.
- Ideally, the supporting beam should match or exceed the depth of the supported beam.
- Prefer W12 and W14 sections for typical gravity columns, as their flange spacing facilitates easier web connections.
By integrating these connection design tips and considering the use of shear plate connections, you can significantly improve the efficiency and cost-effectiveness of your projects. Trusting in the best connection design services in India ensures that your designs are not only optimized but also aligned with industry standards.
For more information, visit www.adept-engineering.com.
To know the latest updates visit our website blogs regularly and also follow our Social Media pages